一、温度与湿度对吸附效果的影响机制
1. 温度的影响
吸附原理:活性炭吸附有机物为放热反应,理论上温度升高会导致吸附容量下降(如苯系物在 25℃时的吸附量比 50℃时高约 30%)。
极端温度风险:
低温(<0℃):气体中水分易凝结,堵塞活性炭孔隙;
高温(>80℃):吸附质分子热运动加剧,脱附速率加快,甚至导致活性炭 “热衰竭”。
2. 湿度的影响
竞争吸附:水蒸气分子(极性)优先占据活性炭表面的极性吸附位点,导致非极性有机物(如 VOCs)的吸附量下降。当相对湿度 > 60% 时,吸附效率可能降低 20%-50%。
物理堵塞:高湿度环境下,活性炭孔隙被水分填充,减少了有效吸附面积,尤其对微孔型活性炭影响显著。
二、温度影响的应对措施
1. 进气温度预处理
高温气体冷却:
安装管式冷却器(如列管式换热器),将进气温度控制在 20-40℃(最佳吸附温度区间);
对于含尘高温气体,可先通过旋风除尘器 + 冷却喷淋塔降温除尘。
低温气体加热:
在冬季或寒冷地区,采用电加热器或蒸汽换热器将进气温度提升至 15℃以上,避免水分凝结。
2. 吸附塔内温度控制
内置温控系统:在吸附层中埋设热电偶,联动调节冷却 / 加热装置,维持塔内温度波动≤±5℃;
选择耐高温活性炭:如煤质活性炭(耐温≤150℃)或特制耐高温活性炭(耐温≥250℃),适用于工业尾气处理场景。
三、湿度影响的应对策略
1. 进气湿度预处理
前置干燥工艺:
采用分子筛干燥塔或硅胶吸附塔,将进气相对湿度控制在 40% 以下;
对于高湿度废气(如涂装线废气),可先通过冷凝除湿 + 气液分离器降低水分含量。
优化进气方式:
采用轴向进气 + 分布板设计,使气体均匀穿过活性炭层,减少局部高湿度区域。
2. 活性炭选型与结构优化
选用疏水型活性炭:
采用表面改性活性炭(如负载金属氧化物或进行疏水处理),降低对水蒸气的吸附亲和力;
优先选择大孔 - 中孔发达的活性炭(如木质活性炭),减少水分对微孔的堵塞。
分层吸附设计:
在吸附塔前端设置预吸附层(填充低成本活性炭或分子筛),优先吸附水分;
后端主吸附层使用高性能活性炭,专注处理有机物。
四、复合工况下的综合解决方案
运行参数动态调整
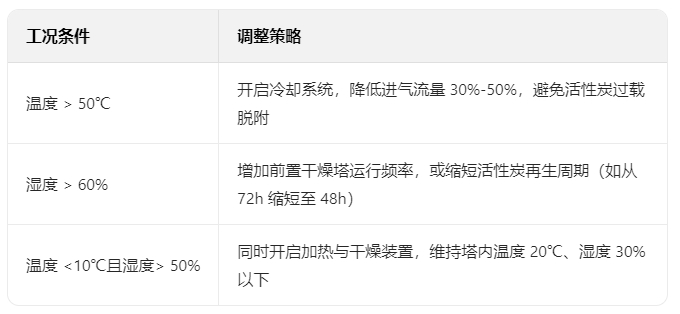
五、运维优化与监测手段
在线监测系统:安装温湿度传感器 + VOCs 浓度检测仪,实时监控进气参数,当温度 > 45℃或湿度 > 50% 时触发报警;
活性炭再生周期优化:高温工况下,将再生温度从 120℃提升至 150℃,确保水分与有机物彻底脱附;
高湿度工况下,增加再生频次(如每周 2 次),防止活性炭长期吸水失效;
备用吸附塔设计:对于关键工艺,设置并联吸附塔,便于在极端工况下切换使用,避免系统停机。
总结
温度和湿度对活性炭吸附塔的影响本质是对吸附热力学与动力学的干扰,需通过 “预处理控参 + 材料适配 + 工艺优化” 三重手段应对。实际应用中,建议根据废气特性(如温度波动范围、湿度峰值)定制解决方案,例如化工行业高温废气可采用 “冷却 + 疏水活性炭” 组合,涂装行业高湿度废气优先 “除湿 + 分层吸附” 工艺,以确保吸附效率稳定在 90% 以上。
|